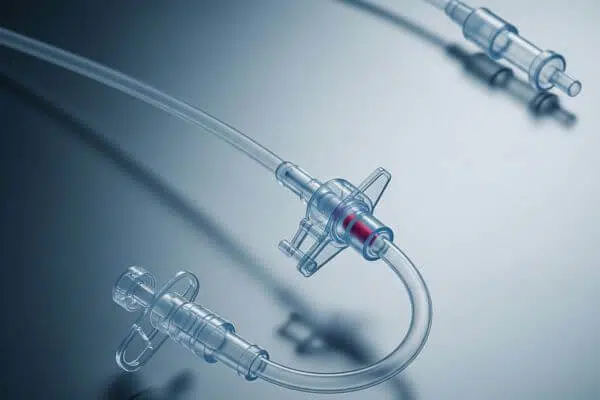
In the medical device industry, the inspection and quality control of plastic components are critical for ensuring safety, reliability and compliance with regulatory standards. These components are frequently used in disposable devices, sterile packaging or surgical instruments that come into direct contact with the patient. They must meet tight dimensional tolerances, have defect-free surfaces, and be manufactured using materials compliant with ISO 13485 and FDA requirements.
The challenge
A primary challenge is the detection of micro-defects such as cracks, inclusions, porosity or contamination, which are often difficult to identify without magnification. Even small imperfections, including inclusions, surface flaws or out-of-tolerance dimensions, can compromise device function or pose a risk to the patient.
Inspection methods
To address this, manufacturers employ advanced quality control processes. These include highresolution visual inspection, precision dimensional measurement and full batch traceability. Inspection systems must deliver reliability, repeatability and efficiency, particularly in highvolume production environments.
Application examples
Common applications include the inspection of Luer fittings and non-return valves, where tolerances below ±10 μm are often required to ensure correct fit and function. Infusion devices must also be checked for microbubbles or surface defects, which can affect flow performance and patient safety. Components such as syringe bodies or polycarbonate flanges may require measurement accuracy of ±2 μm. In many cases, inspection systems must integrate with ISO Class 7 or 8 cleanrooms or operate within laminar flow hoods.
Advanced optical inspection systems help improve quality assurance by supporting defect detection, reducing waste and ensuring compliance with international standards. They contribute to consistent and traceable manufacturing outcomes in the medical sector.
Vision Engineering solutions
Eyepiece-free stereo microscopes such as Mantis and Lynx EVO provide ergonomic advantages and reduce operator fatigue. Digital systems including EVO Cam II and DRV-Z1 support real-time image sharing across teams and sites. Optical and video measurement systems such as Swift PRO and LVC provide accurate and repeatable dimensional checks for non-contact quality control.
Author: Francesca Scarpetta, Marketing Communications Manager
Vision Engineering Ltd Italia